Table of Contents Show
A key element of the strategy of Cobalt Blue Holdings Ltd (ASX:COB, OTC:CBBHF) to provide a reliable supply of responsibly sourced battery metals to the world is the Cobalt in Waste Streams Project (CWSP) in which critical minerals, like cobalt and nickel, are extracted from mine waste.
Processing technology developed and patented by Cobalt Blue is used on the waste to extract the critical minerals, which are essential to lithium-ion battery chemistry.
The Cobalt Blue process also removes acid-forming sulphides to create commercial opportunity through sulphur production.
Environmental benefits
Not only does the process provide commercial opportunities it also reduces ongoing tailings management costs and mitigates potential environmental harm.
The CWSP is one part of COB’s three-pronged supply strategy with the other components being the Broken Hill Cobalt Project in New South Wales and a cobalt-nickel refinery in Western Australia.
Recognising the need to provide a reliable supply of responsibly sourced battery metals, last year the company launched the CWSP with collaborative arrangements underway on tailing sites in Australia and Canada.
Initial test work on the waste material by the CWSP team led by PhD qualified geologist Dr Helen Degeling has produced encouraging results and, as such, has attracted strong interest from Europe.
Large-scale opportunity
It points to COB being on the verge of a large-scale global opportunity identifying opportunities for green metal extraction from mine waste with the company at the forefront of delivering beneficial outcomes.
Dr Degeling, who has more than 18 years of experience in mining, government and academia and a passion for the circular mining economy, said: “At Cobalt Blue we intend to turn this massive mine waste legacy into an opportunity, not only for the mining industry but also for battery manufacturers, local communities and the environment.
“Our mine waste solution has the potential to commercialise discarded metals and leave sites with a smaller volume of benign waste to reduce the overall environmental liability.”
Mining and waste
The world has been mining for clays and metals for tens of thousands of years. Over time, the mining industry has become more sophisticated and productive, creating countless positive impacts for humanity.
Yet, mining also leaves behind an enormous environmental legacy of waste, mostly in the form of tailings dams and spent heaps. Around 10 billion tonnes of global mine waste is produced annually, mostly contained in tailings facilities across the six traditional commodities of alumina, gold, coal, iron ore, nickel and copper.
Copper mining solely accounted for more than one-third of that figure, with 3.4 billion tonnes of tailings produced from copper mines in 2018.
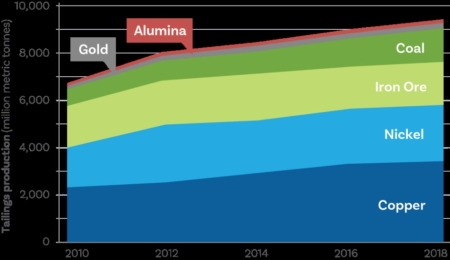
Source – International Council on Mining and Metals; Roadmap for Tailings Reduction, 2022.
The tailings facilities require ongoing management to mitigate potential environmental harm and many contain discarded metals that are important to the Global Energy Transition. Poorly managed facilities can have devastating impacts on ecosystems and communities.
Collaboration is key
Dr Degeling said that the adaptability of Cobalt Blue’s process was important to achieving successful outcomes, with each mine site being different and characterised by variations in mineralogy and chemistry.
She added that collaborative arrangements were ‘key’ to co-creating solutions that could adapt to local conditions and would prove to be of most benefit to mining companies, governments, communities and the environment.
Cobalt Blue sees an enormous opportunity contained in this waste, where traditional mining value chains have instead viewed it as a liability.
Powering energy transition
Demand for metals and critical minerals is increasing as the world turns to EVs and battery storage to power the Great Energy Transition.
The new US Inflation Reduction Act (IRA) and EU Critical Raw Materials Act (CRMA) will significantly impact the global critical minerals supply chain through the provision of incentives for the supply of responsibly sourced materials.
With most of the world’s cobalt coming from China and the Democratic Republic of the Congo, the global race to secure IRA- and CRMA-compliant supply is rapidly advancing an Allied Nations critical materials supply chain, including the US, EU, Japan, South Korea, Canada and Australia.
Yet, the global decline in grades of metalliferous mines worldwide is creating a shortage of supply, especially for metals essential to the Energy Transition, such as nickel and copper, which means more material is being mined to produce the same volume of metal, thus increasing the quantity of waste being stored year-by-year.
On the scale of the opportunity in Australia, it is estimated by the Cooperative Research Centre for Transformations in Mining Economies (CRC TiME) in a report on ‘Enabling Mine Closure and Transitions’ 2023) that around 240 mines are due to close across Australia by 2040 and tens of thousands of mines remain un-rehabilitated in Australia alone.
Interest from Europe
“The prospects are even larger in Europe and that’s why we are seeing such strong interest arising from the EU, where EuroGeoSurveys have defined over 20,000 active and inactive mine sites, representing thousands of years of mining,” said Dr Degeling.
“This presents an enormous opportunity for us to revisit these sites and lead a new frontier in critical metal exploration to create a positive legacy out of what has gone before.”
COB CEO Joe Kaderavek said the company was ready to address the enormous opportunity contained globally in mine tailings.
“Solving an enormous problem”
“We have validated and optimised our technology through processing cobalt-pyrite ore from our Broken Hill Cobalt Project to generate cobalt sulphate for battery manufacture and elemental sulphur for agriculture,” he said.
“Our team at the Demonstration Plant in Broken Hill is the first in the world to develop and apply this process.
“This expertise has been established in Australia and can be taken worldwide to solve an enormous problem that contains immense opportunity.
“Not only can we extract metals essential to batteries, but we can also remove acid-forming sulphides to reduce ongoing management costs and potential for environmental harm.”
Originally Posted Here